DJI Osmo Action 5 Pro Battery Life Test
My quest for the longest lasting battery in an action camera has brought me to the DJI Osmo Action 5 Pro and I tested 11 batteries to see how long they would last. Why do I care about long battery life? I race sailboats and when I’m sailing I can’t always stop and change a battery in the middle of a race and sometimes I don’t even have a pocket to keep one in let alone keep it dry.
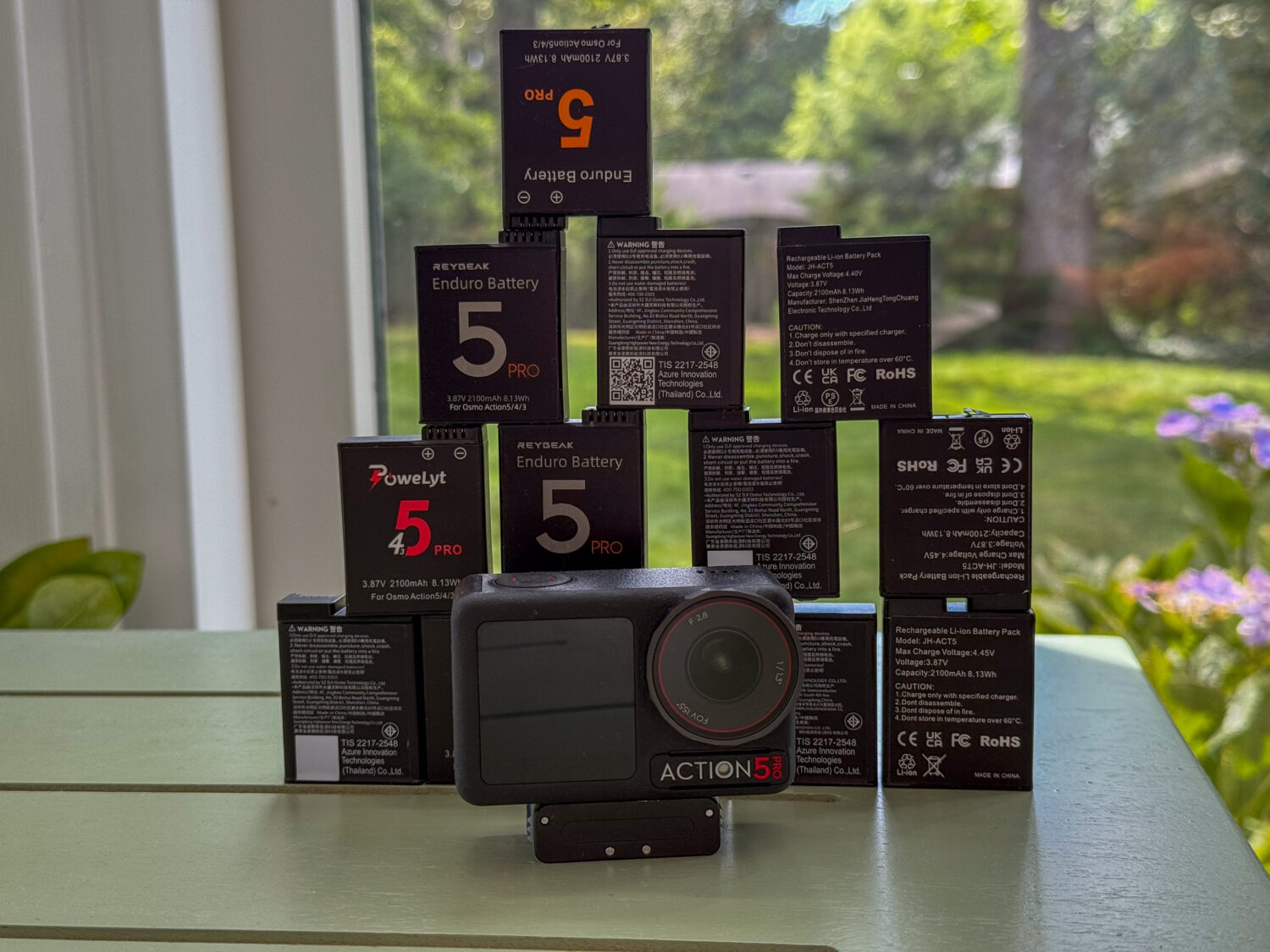
In looking at the cameras on the market the DJI Osmo Action 5 Pro had the best specs for how long it would last using the settings I would want to use while sailing. I wanted to see how long I could expect the two different batteries that are offered by DJI and several different batteries by 3rd party manufactures.
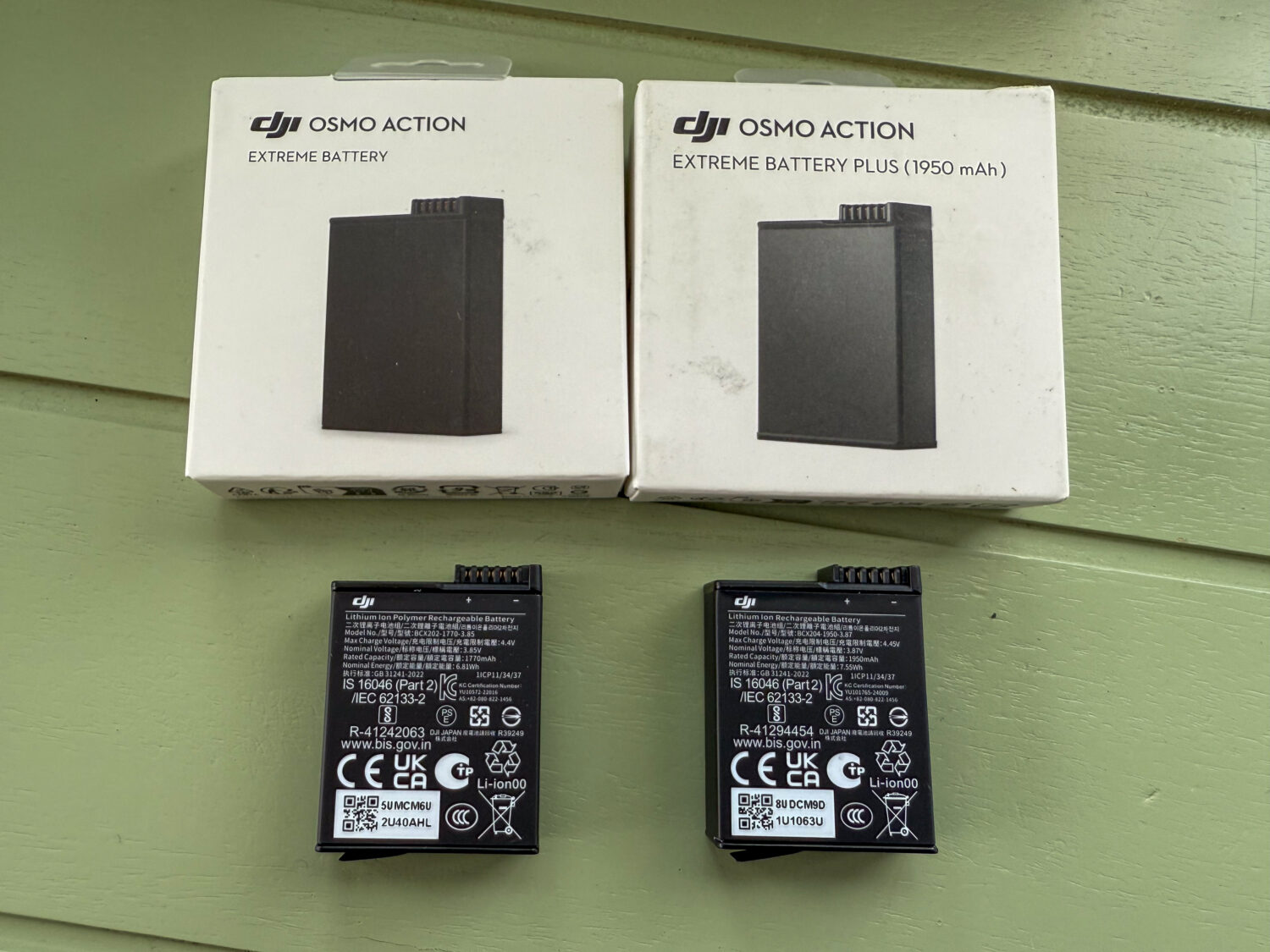
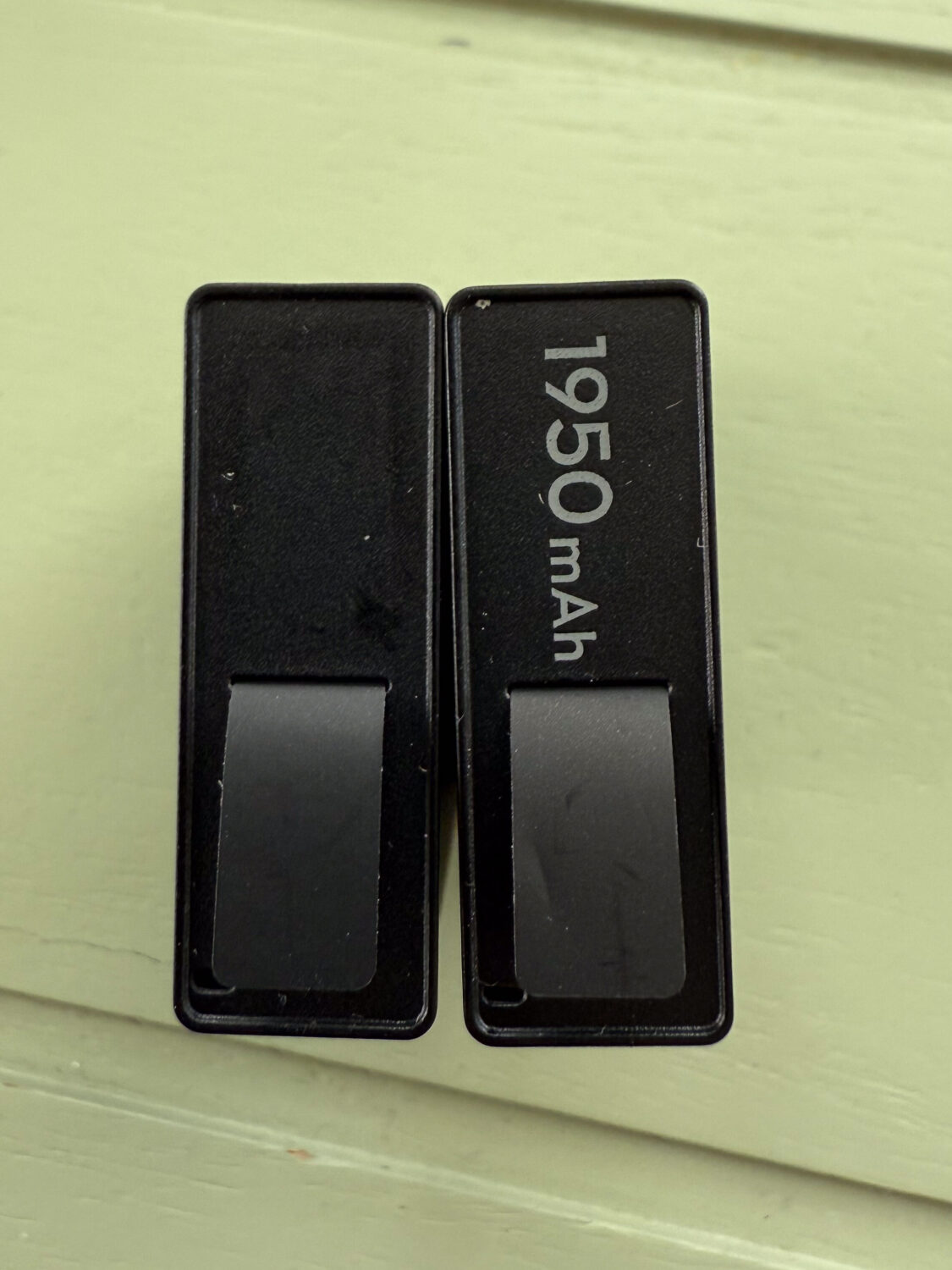
DJI offers the DJI Osmo Action Extreme battery with 1770 mAh that they sold with the Action 3 and 4 and it’s compatible with the Action 5 Pro. And when they came out with the Action 5 Pro, they also came out with an Extreme Plus battery with 1950 mAh. The batteries look identical aside from the very tiny mAh number on the back and the much more obvious 1950 mAh label on the top.
How long does the DJI Osmo Action 5 Pro Battery Last?
Across all of the manufactures, the camera filmed on average for 129.4 minutes. But the DJI batteries far out performed the after market batteries by almost 30 minutes in the case of the Extreme Plus.
Average Duration | |
DJI Extreme Plus | 150.4 min |
DJI Extreme | 138.8 min |
Aftermarket Batteries | 122.4 min |
Which Battery Lasted Longest?
If battery life is of the utmost importance – you’ll want to go with the DJI Extreme Plus Batteries. If you want to save some money, don’t need as long of a duration or can switch batteries easily then the aftermarket batteries will work fine.
Here’s the average runtime for each of the brands:
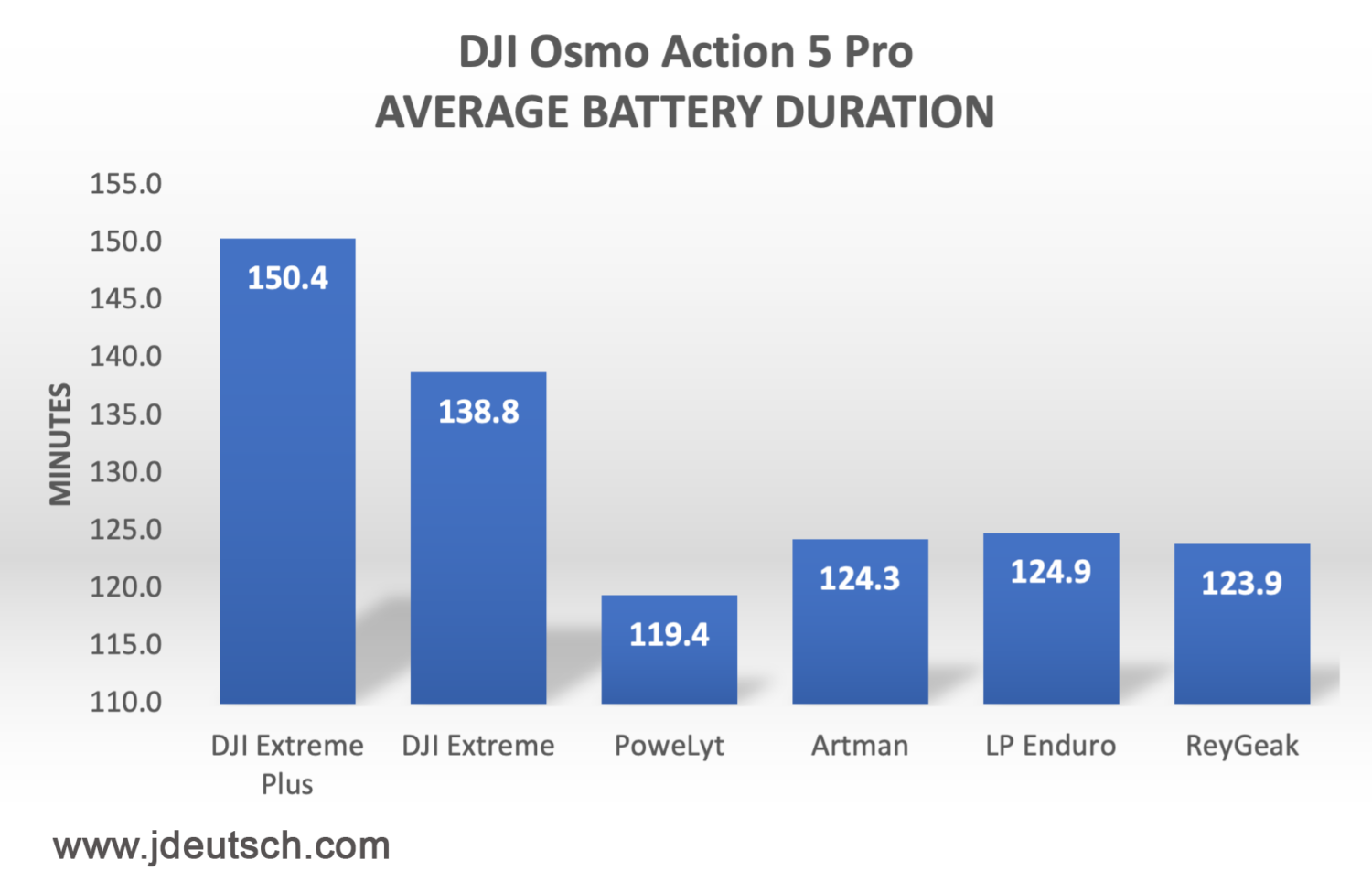
And here you can see the individual performance of each of the batteries. Note the range between the minimum and maximum test along with the average. The DJI Batteries (Extreme & Extreme Plus) minimum performance was at or above the max of most of the 3rd party batteries.
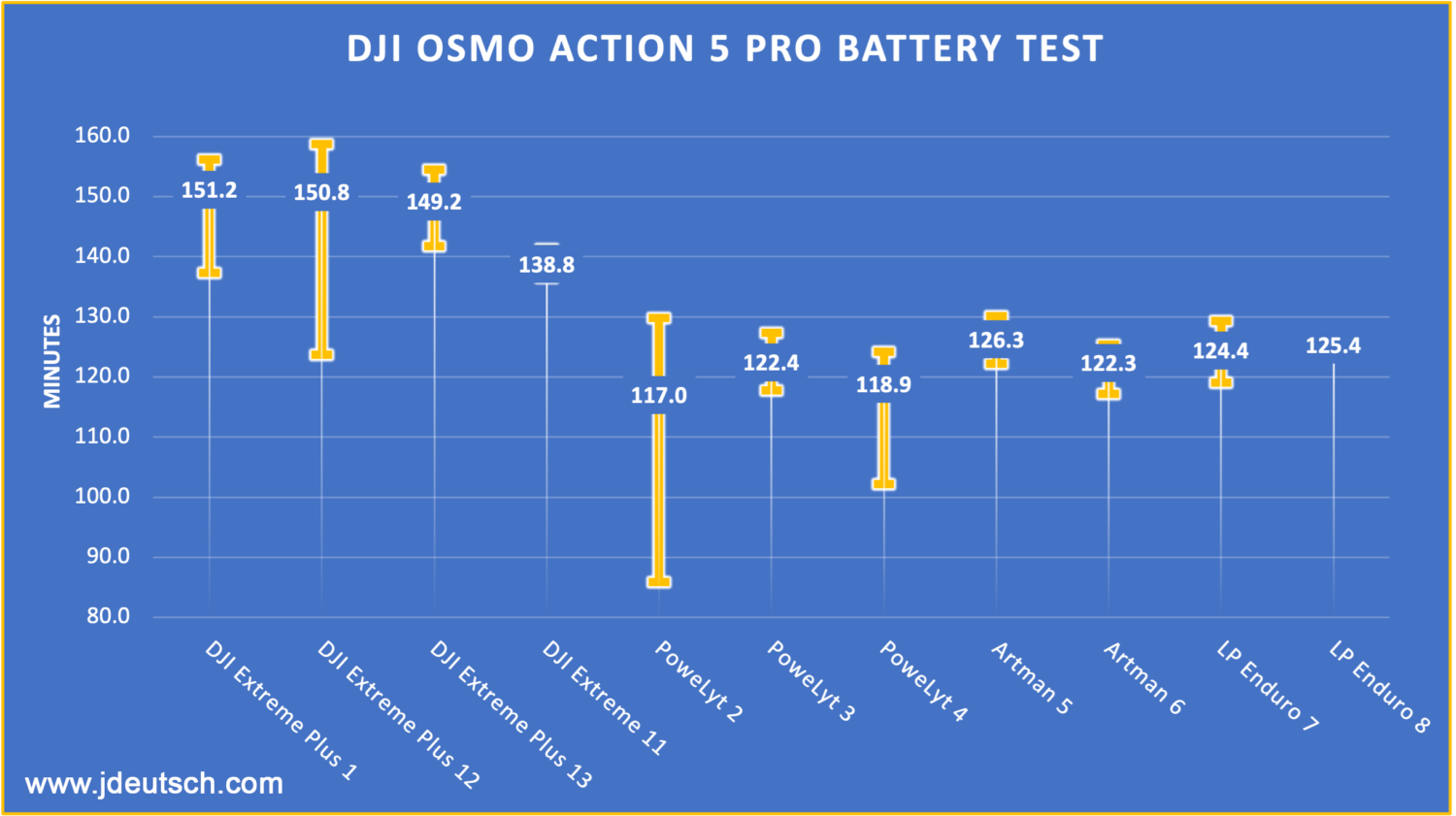
The Batteries
How did I test?
Using the settings I’d most likely be using for sailing – 4k 30 fps with RockSteady and Horizon Steady on and in the wide view – I set the camera up in my living room to look at my backyard until it ran out of battery. I did this at least 11 times for each battery to get the data. All of the batteries were charged using the same 3-battery charger and the DJI firmware was 10.00.11.62 or 1.00.12.12.
To see my videos created with the Insta360 Ace Pro – check out No Quarter Sailing on YouTube.
If you are interested in the battery life of other cameras, check out the tests I did for the Insta360 X4 or Insta360 Ace Pro.
Disclaimers: I purchased the camera and some of the batteries myself. Other batteries were received through the Amazon Vine Voices Program. As an affiliate in Amazon’s program I may receive a commission for product links.